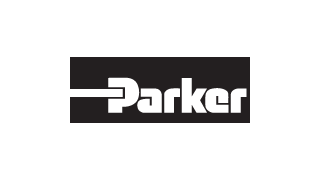
Search the internet for Iron Boat and you’ll most likely come across a number of rib type sports boats with toughened sections to withstand harsh conditions. That’s not what we are building. We’ve derived the name Iron Boat from the Iron Bird test rigs used extensively throughout the aviation industry.
An Iron Bird is a ground based test rig used for prototyping and integrating aircraft systems installed on the rig so their functions can be tested both individually and in conjunction with other systems. The components are usually arranged in roughly the same layout as they will be on the final aircraft but easily accessible for maintenance. Some Iron Birds also include a flight deck so that testing can include pilot inputs and simulated flight profiles. It can also be used for pre-flight pilot training.
Thanks to a relationship with key people at Parker UK we are pleased to say that the build and operation of a ThrustWSH Iron Boat test rig will happen at our workshop in Suffolk. We will be fully supported with product and technical backup by Parker Hydraulics through the entire ThrustWSH project. This means that they will supply all hydraulic parts plus electrical and electronic parts in support of the hydraulic systems that will eventually provide ThrustWSH C6 with full stability control and steering systems including the pilot in the loop interface. But before then, everything will be developed and tested on an Iron Boat test rig.

We have already been provided with a hydraulic ground support unit and its cooling fan plus a range of other components. Most of the critical components will be coming from Parker’s aerospace product range and will centre around 100 Hz servo valves as used in aircraft control surface actuation. This is critical for us since the key to control and stability at high speed are the movements of the super-cavitating microfoils along with the rear foil struts for steering. The basis of the control system is a Parker IQAN unit which means that electronic control signals can be translated into signals to move actuators via the hydraulics. The signal inputs can be manual via controls to be used on C6, outputs from the control systems tested on the Ugly Boat for C3.2B Test Boat operations, or fully automated as an output of a computer based Six Degrees of Freedom (6DoF) model. Put simply, a computer simulation model operates all the controls as if they were from a pilot before a pilot is then put in the loop to control things manually via fly-by-wire controls.
There will be more about this as things develop but it’s another example of extensive testing being used to ensure that the final design is stable and controllable at speed.
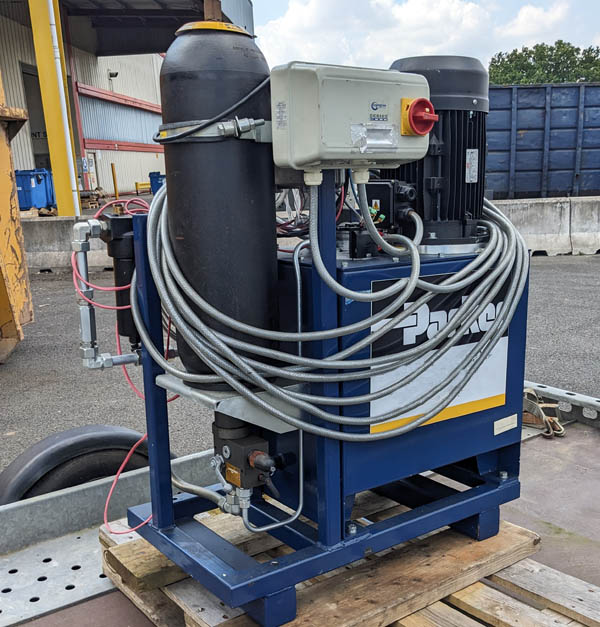